In January 2023, Professors Willy Shih and Mike Toffel led more than 40 HBS MBA students on site visits to witness the energy transition and innovative sustainable production activities throughout Denmark and the Netherlands, in their new Immersive Field Course (IFC). This is one of 13 student essays posted on the HBS Business and Environment Initiative’s Blog that highlights their reflections. Learn more about this IFC course on Decarbonization and Sustainable Production by watching this five minute video summary.
Visit Date: January 12, 2023
As part of the Immersive Field Course (IFC) on Decarbonization and Sustainable Production, our group visited Van den Ende Rozen, a family business located in Monster, near The Hague and Rotterdam in the Netherlands. The company leverages greenhouse technology and digitalization to optimize and scale the business, producing 28 million stems of top quality Red Naomi roses per year.
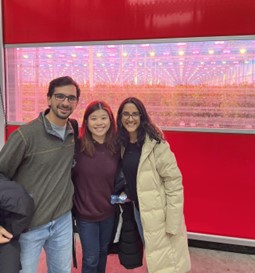
Our day started in Rotterdam, the base camp for all our visits in the Netherlands during the IFC’s second week. On the hourlong bus ride to the greenhouse production site, as we neared the site, we noticed hundreds of small greenhouses alongside the road. From their signage, the crops ranged from vegetables to flowers. We had driven into the heart of the country’s world-class horticulture industry and finally arrived at Van den Ende’s enormous 4.5 hectare (11.1 acre) greenhouse.
Currently in its fourth generation, the company is run by three Van den Ende brothers: Sam, Tim and Bob. They gave us a quick overview of the greenhouse and the processing hall with an automated production line capable of processing 10,000 roses per hour! Operations run 24x7, where the roses are trimmed twice per day, and stems are cut around every seven weeks, aided by cameras installed throughout the facility. The brothers shared the complexity of balancing sustainability and optimization of producing roses, which demands lots of heat and power.
Transition to LED lighting
Van den Ende Rozen currently cultivates only one kind of rose: the Red Naomi. With 60 petals per bloom, it is the top-selling rose in Europe, famous for its intense color, large flower head, subtle fragrance, elegant long stem, outstanding transportability and long shelf-life (which lasts from 2 to 2.5 weeks).
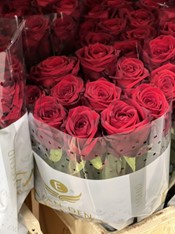
Five years ago, the brothers started to test the optimal intensity and spectrum of LED lighting on rose cultivation in an experimental site, recognizing that yellow light simulates sunlight, and red light promotes faster growth. Three months ago, they replaced some lights with LEDs in their greenhouses with good results. Prior to the replacement, lighting consumed 12 megawatt-hours per day. The greenhouse shuts down all lights for approx. four hours per day because plants need rest. Switching some lighting to LED reduced electricity use by 40%.
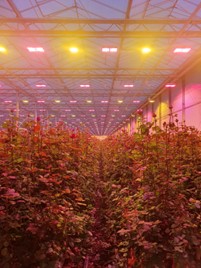
Finding the right spectrum continues to prove challenging. The business’s effort to transition to all LED lighting showed poor results (the rose petals turned black). Additionally, unlike incandescent lightbulbs, LED produces only light not heat, although both are crucial to rose cultivation. To compensate for reduced lightbulb heat, they purchased an extra generator, which increased energy consumption. Lastly, LED lights and adjustments in lighting lead their cameras to malfunction. As the cameras monitor and collect data used to make recommendations about which roses to cut, they need to function properly to optimize production.
While challenges persist, the brothers continue to test lighting options with a target of switching their greenhouses entirely to LED in the next two years.
Digitalization and Automation
The site we visited was Van den Ende Rozen’s second and newest greenhouse. Constructed in 2008, the site covers 80,000 square meters, capable of yielding over 300 roses per square meter per year. The operation’s three cost drivers are energy, labor, and facility management. To improve scalability and production efficiency, they installed a chip system throughout the rose garden. Before cutting the roses, the growers use a chip sensor that helps monitor the quality of the roses, and record the grower responsible for cutting the roses and the speed at which they are harvested.
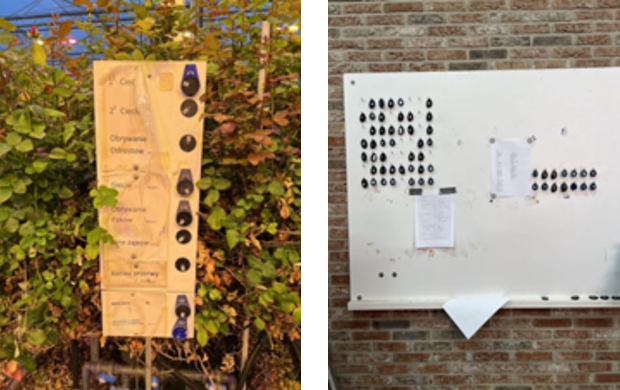
This digitalization strategy allows the company to monitor the harvesting progress, collect and gather data and continuously improve production results, which in turn increases standardization, efficiency and scalability.
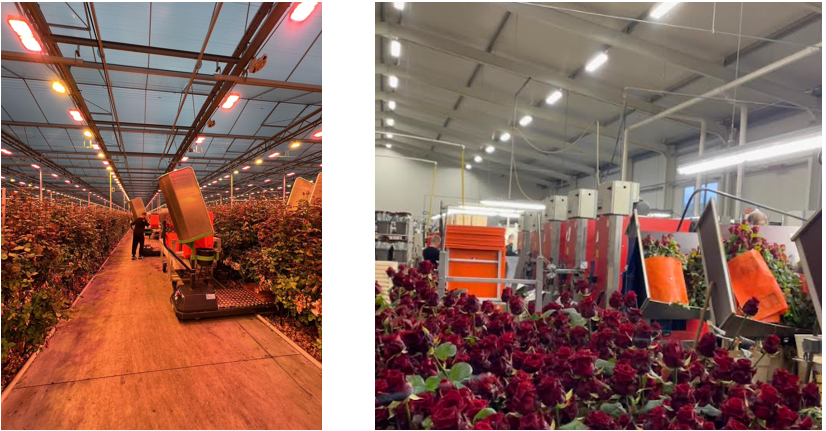
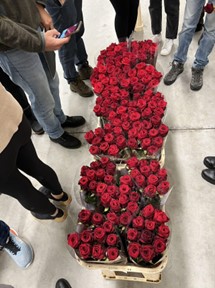
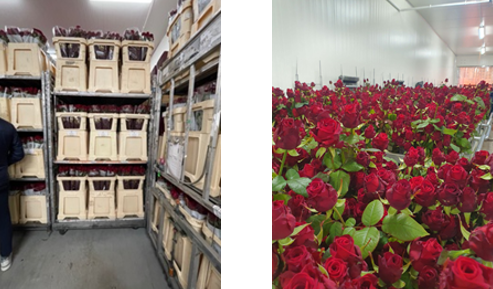
Energy and Resource Consumption
The facility is currently heated by natural gas, where prices have been locked in through long-term contracts. They were able to lock in gas prices before the Russian-Ukraine war and have benefitted from very low cost during the winter, while some of their competitors had to stop producing because they could not purchase natural gas due to the sudden price escalations.
The site’s electricity was contracted three years ago, which saved them from incurring the much higher prices since the Russia-Ukraine war began. Over the past four years, the company has explored alternative energy sources, but found the cost of renewables to be far too expensive to justify. They continue to explore alternative energy sources such as wind, solar and hydrogen.
The company also is examining ways to reduce their chemical use. Onsite, they use cats (five!) to keep rats out of the facility without using rat poison. They primarily rely on “good insects” that eat “bad insects” in order to minimize pesticide use, and they constantly test pH levels and mineral content in the water delivered to the roses. 50-60% water used in the farm is reused after going through UV treatment. Dead leaves are left on the floor since they release CO2, which is later consumed by the roses.
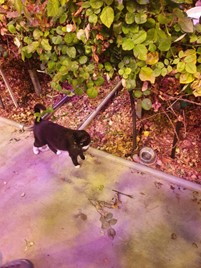
We were surprised and impressed by the level of sophistication and technology involved in rose cultivation. Next time we purchase a bouquet, we will definitely be thinking about everything going on beyond the price tag.
Read more posts in the IFC Series:
Deconstructing LEGO’s Decarbonization
Port Esbjerg: Deploying Offshore Wind
HySynergy and Crossbridge Energy
Grundfos: Innovation & Inspiration for Sustainable Product Design
Arla Foods: How Sustainable Can A Dairy Company Be?
Amager Bakke: A Look into the Future of Waste Incineration
Maersk’s Journey to Decarbonize Shipping
BTG Bioliquids: Creating Fast Pyrolysis Bio-Oil from Biomass Residue Streams
Grolsch Brewing Company: Drink Sustainably
Van den Ende Rozen: Greenhouse Rose Production