In January 2024, Professors Willy Shih and Mike Toffel led 45 HBS MBA students on site visits to witness the energy transition and innovative sustainable production activities throughout Denmark and the Netherlands, in the second year of their Immersive Field Course (IFC). This is one of nine student essays that highlight their reflections.
When we visited LM Wind Power’s Test and Validation Center in Lunderskov, Denmark, we saw how they work to optimize the efficiency and safety of their blades through a variety of testing approaches.
Company Overview
The company specializes in providing the most cutting-edge technology and highest quality turbine blades, which it sells to companies such as Vestas, Siemens, and GE, LM Wind’s parent company.
Below is a photo of our team in front of the first-ever offshore wind turbine blade built in 1991, when many believed that turbine blades could not get any larger. However, as of 2019, new blades measured up to 107 meters long, or 8 times longer than the blade shown in the picture! With each incremental increase in the length of the blade, the swept area of the wind turbine increases by the blade length squared (proportional to the area of a circle). The amount of energy that can be captured by the blades on a turbine are proportional to the swept area.
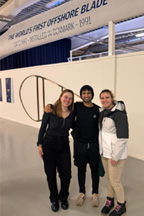
With blades growing longer and longer, LM Wind has expanded their engineering capabilities and moved to new materials, such as carbon fiber, to withstand the significantly higher loads. The Test and Validation Center is used to design and validate these new blade structures and materials.
Testing Facilities
Testing in-house is faster than via an outsourced provider, which enables the company to more rapidly iterate on their designs. LM Wind’s testing facilities perform static and dynamic testing, rain erosion testing, and aerodynamic testing using the only wind tunnel owned by a turbine blade manufacturer. These testing facilities allow the company to remain competitive in a rapidly evolving market.
When a blade design is finished, it is first tested statically (a load is applied slowly to the blade). The static load that is applied is calculated to be the realistic maximum load that the blade may experience in the field, or a worst-case scenario. After the blade withstands this maximum load for 10 seconds, it moves on to dynamic testing.
In dynamic testing, the blade is cycled along a single axis while the end is fixed to a large concrete structure that extends far into the ground. The blade is cycled to mimic at least 20 years of life in the field, meaning that it experiences between 1.5 and 2 million bending cycles, which may take months, or even years, of test time. Throughout the course of the test, the blades are inspected with infrared light to detect damage or defects in the blade structure. Upon completion of the dynamic test, the blade then repeats static testing to ensure that it remained structurally sound.
In some cases, LM Wind performs destructive testing, which it calls a crash test. In a crash test, the company applies load to the blade up until the ultimate strength and records the force required to catastrophically break the blade (resulting in a big mess and a loud noise!).
LM Wind’s wind tunnel was impressive. Capable of wind speeds up to 380 km/hr, the test measures the lift, the drag, and the moment on the blade at different wind speeds and pitch. The test equipment uses pressure sensors located throughout the wind tunnel and on the blade itself. The wind tunnel data forms half of the company’s iterative aerodynamic design cycle. Combined with the use of simulation tools, design engineers get a full picture of the blade design.
Finally, the facilities also include a rain erosion testing facility that is used to assess various protective coating materials to be used on the blade. These materials are known as “leading edge protection.” Without a coating on the blades, raindrops would begin to erode the blade and result in significant damage over time.
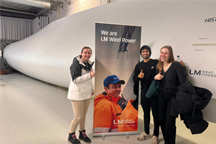