In January 2024, Professors Willy Shih and Mike Toffel led 45 HBS MBA students on site visits to witness the energy transition and innovative sustainable production activities throughout Denmark and the Netherlands, in the second year of their Immersive Field Course (IFC). This is one of nine student essays that highlight their reflections.
As the world races towards a sustainable future, renewable energy solutions are at the forefront of this crucial transition. Vestas, a global leader in wind turbine manufacturing since 1989, stands as a beacon of innovation in this change. Recently, our team had the incredible opportunity to visit Vestas' state-of-the-art factory in Odense, Denmark where the company manufactures its cutting-edge 9.5 MW (model V174) and 15 MW (V236) offshore wind turbines intended for installations around the world.
Inside the Wind Turbine: A Tour of a Manufacturing Marvel
Over the course of a chilly Danish morning, our group of 45 students had the opportunity to interact with leading Vestas engineers, learn about the company’s latest offshore wind efforts, and tour its manufacturing facility, tracking the development of an offshore wind turbine from start to finish. We were able to physically walk through the process from the intake of turbine components and parts through gearbox assembly, nacelle engineering, hub construction, and blade installation.
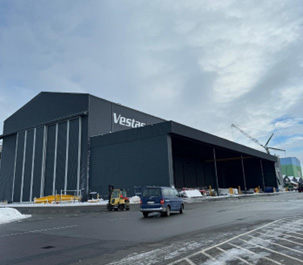
The highlight of our visit was an immersive tour through the intricate manufacturing process of Vestas' V174 nacelle, a vital component of the 9.5 MW wind turbines. The nacelle, a housing unit that encapsulates the generator, gearbox, and other key generation and safety components, is the powerhouse of the wind turbine.
Our group had the privilege of physically going inside the nacelle, witnessing firsthand how each component fits seamlessly together. Donning personal protective equipment, steel-toed boots, and hard hats, we ascended over 15 feet of ladders into the high-tech nacelle body for a full 360-degree walk around view of the inner gearbox and generator. We were also able to climb the inner staircase to reach the roof of the nacelle for a view of the helipad used for operations, maintenance, and servicing.
The sheer scale and complexity of the manufacturing process left us in awe. The nacelle we observed was destined for an offshore wind field in Taiwan, emphasizing Vestas' global reach and impact in the renewable energy ecosystem.
There were several interesting takeaways from the Vestas manufacturing process. First, the entire factory synchronizes manufacturing assembly timelines such that each step in the process is aligned to last the same amount of time, ensuring a seamless transition to the next production step. Even if steps could be completed more quickly, they are held constant to ensure quality and avoid process bottlenecks. This orchestration showcased Vestas' commitment to precision in delivering top-notch wind turbines to power the world sustainably.
Second, we were impressed by Vestas’ commitment to quality and efficiency. After our first year course in operations management, we were excited to see process design principles in action. Weekly Kaizen and 5S (Sort-Set-Shine-Standardize-Sustain) reviews demonstrate the company’s commitment to process improvement and excellence. The meticulous process standardization and data tracking of both components and process efficiency was impressively coordinated at such a massive scale.
Finally, we learned that Vestas tests each turbine to ensure it can withstand extreme weather conditions without interruption, stressing each component at 3x the expected load. Vestas discussed their unique partnership structures with their customers and suppliers to ensure the safety and quality of all of its products.
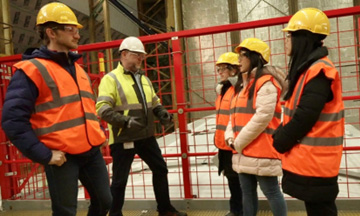
Cultural Dynamics: A Danish Approach to Work-Life Balance
Beyond the impressive machinery and manufacturing prowess, this visit also gave us unique insight into the cultural dynamics that define Vestas' workplace in Denmark. The Danish workers, we learned, exhibit a unique satisfaction with their jobs. In a country renowned for its emphasis on work-life balance, Vestas takes it to another level – employees work a maximum of 35 hours per week, although we met many people who noted they work longer because of their passion for their jobs.
We were struck by the lack of strict guidelines on breaks or vacation. Instead, Danish workers operate with a sense of responsibility and autonomy, knowing when to complete their tasks efficiently. This approach fosters a work environment where individuals take ownership of their roles, contributing to the overall success of Vestas in the renewable energy sector.
Conclusion: A Student's Perspective on Climate Change and Vestas' Impact
Our visit to the Vestas site was highly inspiring in many aspects. The meticulous manufacturing process and understanding of cultural dynamics emphasized the crucial interplay between technology and human collaboration in driving sustainable change. Vestas demonstrated itself to be more than a mere wind turbine manufacturer: it stands as a pioneer in the global fight against climate change. Vestas exemplifies the fusion of cutting-edge technology with a work culture valuing employee well-being. As students passionate about addressing climate change, the visit instilled more excitement for renewable energy advancements and hope for a future where sustainability is a global priority. In conclusion, the journey through Vestas' wind turbine manufacturing facility illuminated a path toward a cleaner, greener world.