In January 2024, Professors Willy Shih and Mike Toffel led 45 HBS MBA students on site visits to witness the energy transition and innovative sustainable production activities throughout Denmark and the Netherlands, in the second year of their Immersive Field Course (IFC). This is one of nine student essays that highlight their reflections.
After spending the morning at the Royal Flora Holland auction house, we traveled from Amsterdam to Monster where we were welcomed to Van den Ende Rozen by two of the three brothers who run the company, Tim and Bob Van den Ende. It was clear from the start that the family dynamic of the brothers creates a playful, supportive, and competitive work environment as each brother is responsible for a different area of the business.
We started our tour of the facility by walking into the warm, brightly lit 4.5-hectare greenhouse where the company grows its Red Naomi roses. In the mornings, the greenhouse’s production team works on cutting and pruning the roses, while the afternoons are focused on processing and packaging. During the growing stage, the rose plants need to be pruned or cut very often. After a rose is cut, it takes six to seven weeks for a plant to grow a new flower. The total capacity of the 4.5-hectare greenhouse is 400 roses/m² per year. The growers use a mix of extensive experience and technology to efficiently grow a high-quality product. Throughout the greenhouse, there are 17 different environmental sensors that track everything from temperature to light intensity and humidity.
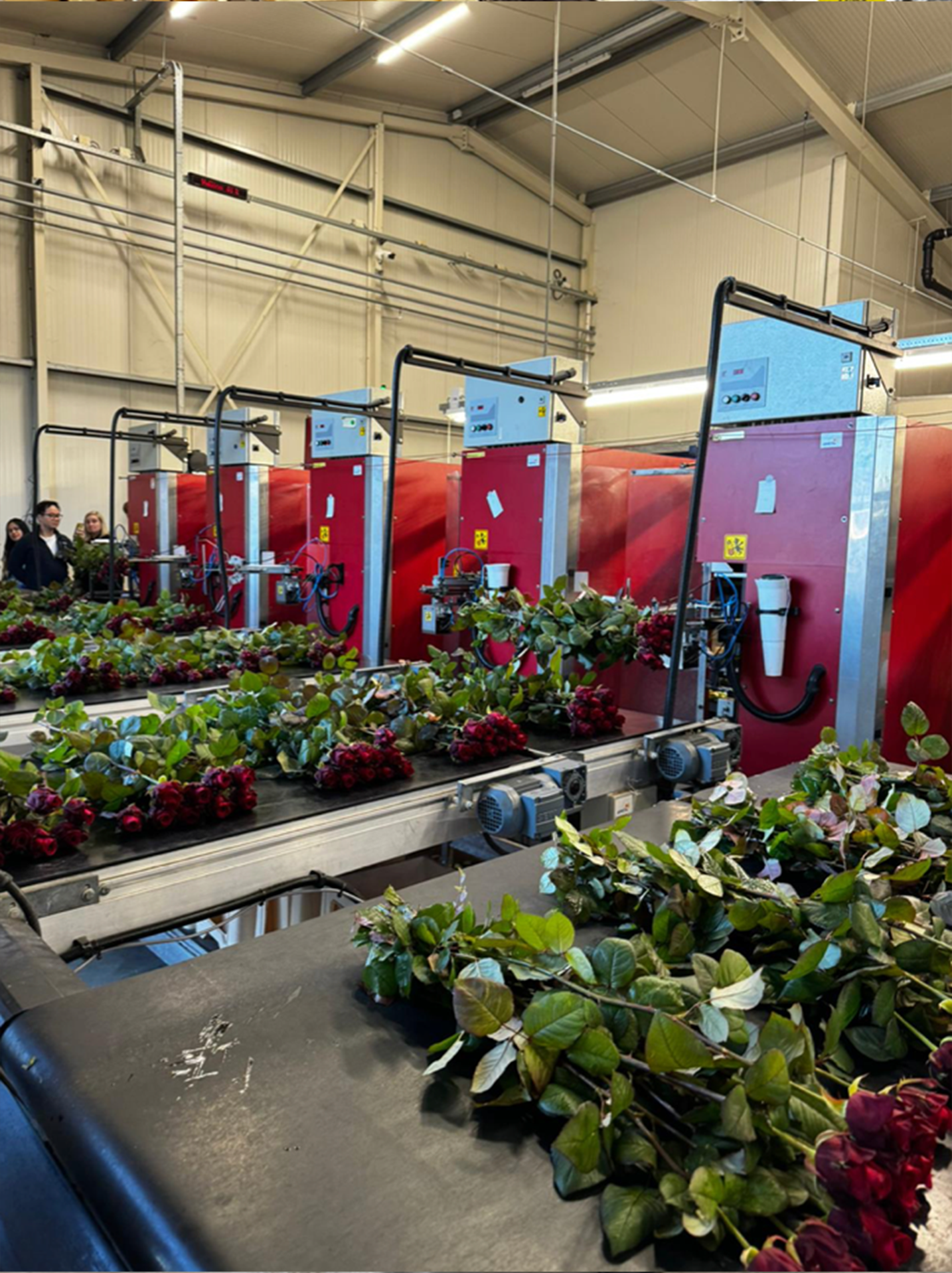
Once cut, the flowers are handled differently depending on the tastes of the customer. For example, some regions such as Scandinavia prefer their flowers to have more natural greenery so they have more control over the final appearance of mixed bouquets. Van den Ende Rozen sells 65% of their flowers directly to customers such as grocers and convenience stores, while the rest is sent to auction houses like Royal Flora Holland. The price at the auction house determines the price for direct sales as well. While it’s difficult to create a consumer-recognized brand of flowers, Van den Ende Rozen still strives to produce the highest quality of roses for all to enjoy.
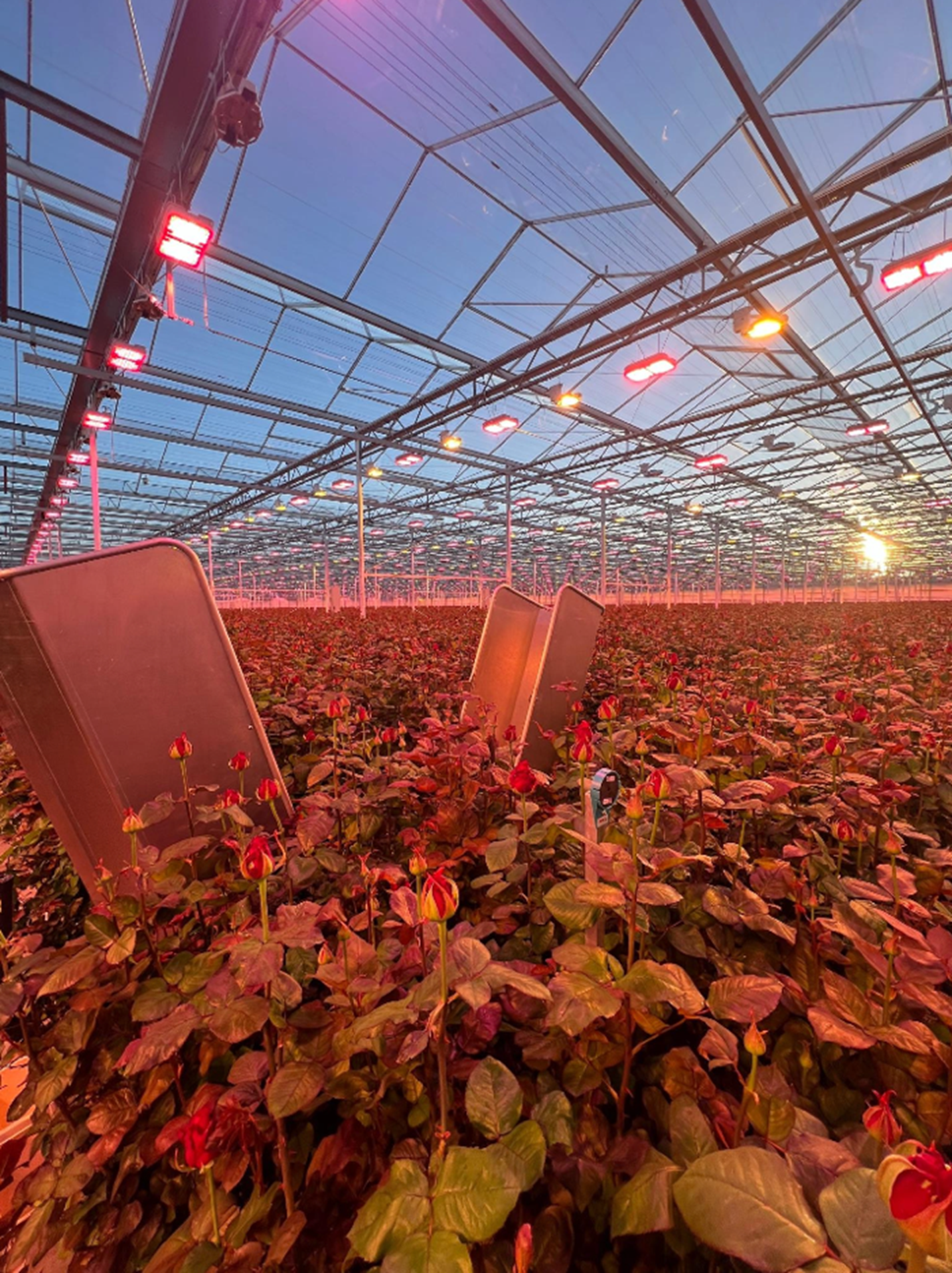
Sustainability
Throughout the tour, the Van den Ende brothers touched upon multiple aspects of sustainable agriculture that have been integrated into their greenhouse. Within the past year, 50% of their greenhouse lighting has been transitioned from incandescent lighting to LEDs, which emit a light spectrum that is optimized for rose growing. The transition has reduced energy use by 50% but has also caused a reduction in the amount of heat emitted into the greenhouse. Natural gas heating has been employed to compensate, adding additional pressure to the operating costs of the business due to price increases because of the Russia-Ukraine war. The Van den Ende brothers shared their plans to implement geothermal heat pumps for the greenhouse within the next two years in order to reduce and then eliminate the use of natural gas. Additionally, within the harvesting process, 50% of the water used in rose cultivation is captured, treated with UV light, and reused for future crops.
The Van den Ende brothers also continue to explore ways to reduce the use of chemical pesticides. They have already transitioned 90% of their greenhouse to biological pest control systems, wherein living organisms that are natural enemies of invasive insects are distributed throughout the rose crop in order to prevent infestations and damage to the flowers. This number is expected to increase to 100% nature-based pest control as EU legislation moves to eliminate the use of chemical pesticides within the next decade. Instead of using rodenticides, several cats live in the greenhouse to control the mice population.
The company extends its commitment to sustainability throughout its entire supply chain. This includes employing electric cars for harvesting roses and procuring residual carbon dioxide for the greenhouses from a Shell refinery in Rotterdam. During the transition from gas-based heating to geothermal energy, the company also buys green power for their existing 15MW electric cogeneration facility.
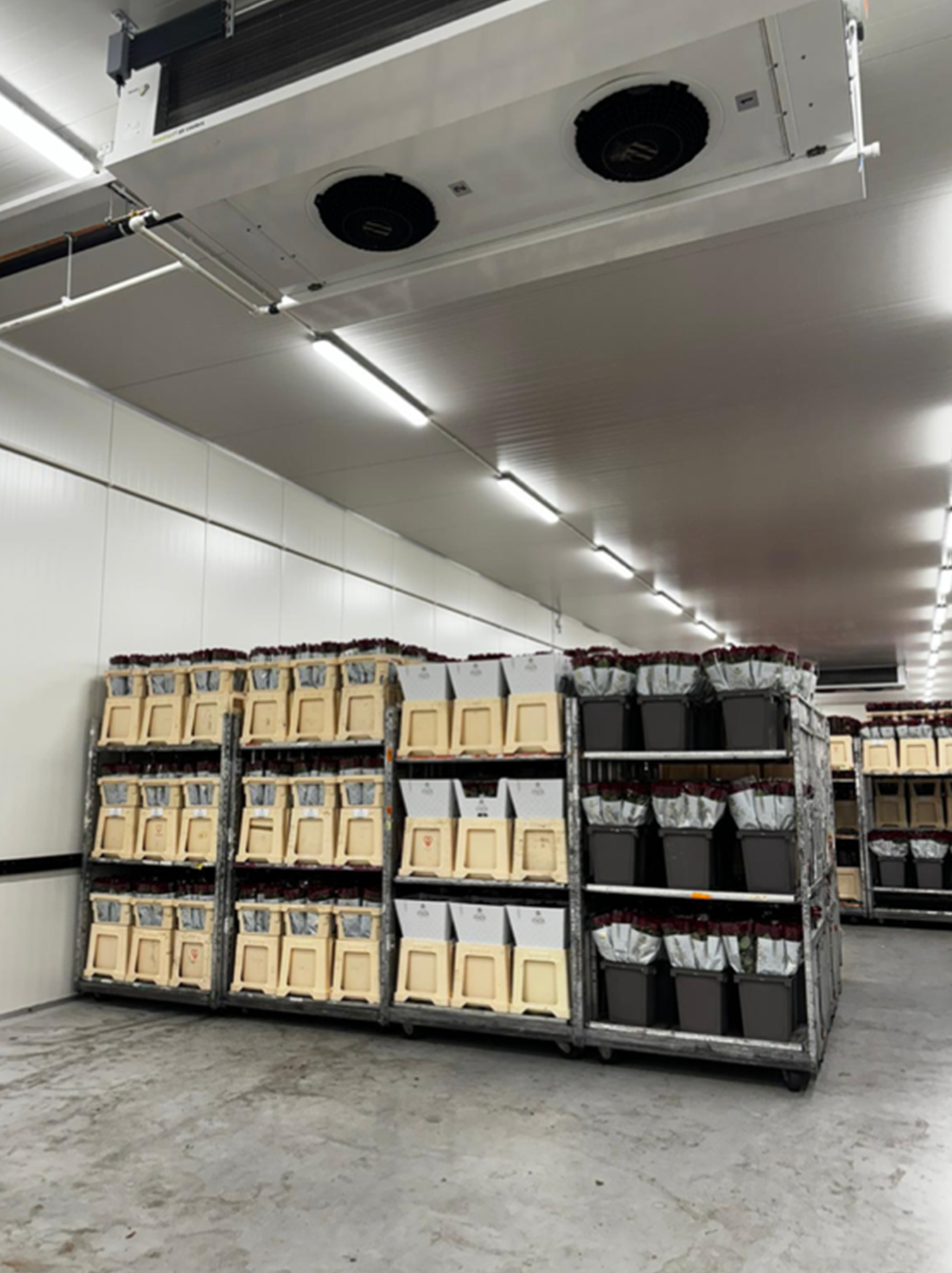
Interesting Learnings & Future Challenges
Examining this century-old family business, we noted its adaptability to market shifts. Initially focused on growing vegetables, the shift to specializing in roses was compelling, so we delved deeper into the decision. The Van den Ende brothers explained how optimization for a single crop enhanced both yield and sustainability. In today’s context, auction houses are considering implementing systems to reveal flower carbon footprints that could reshape rose demand, adding an environmental factor to consumer choices.
In discussions with the Van den Ende brothers, the timeline for integrating geothermal energy emerged. The goal is to commission the plant in 2024, but the facility's construction is controlled by the local government. The geothermal installation shares infrastructure with the neighboring plant. This highlights a crucial aspect of sustainable tech transition: it's not only about technology and costs but also about policy and government support. The interplay between private ambitions and regulations impacts the pace of embracing sustainability.
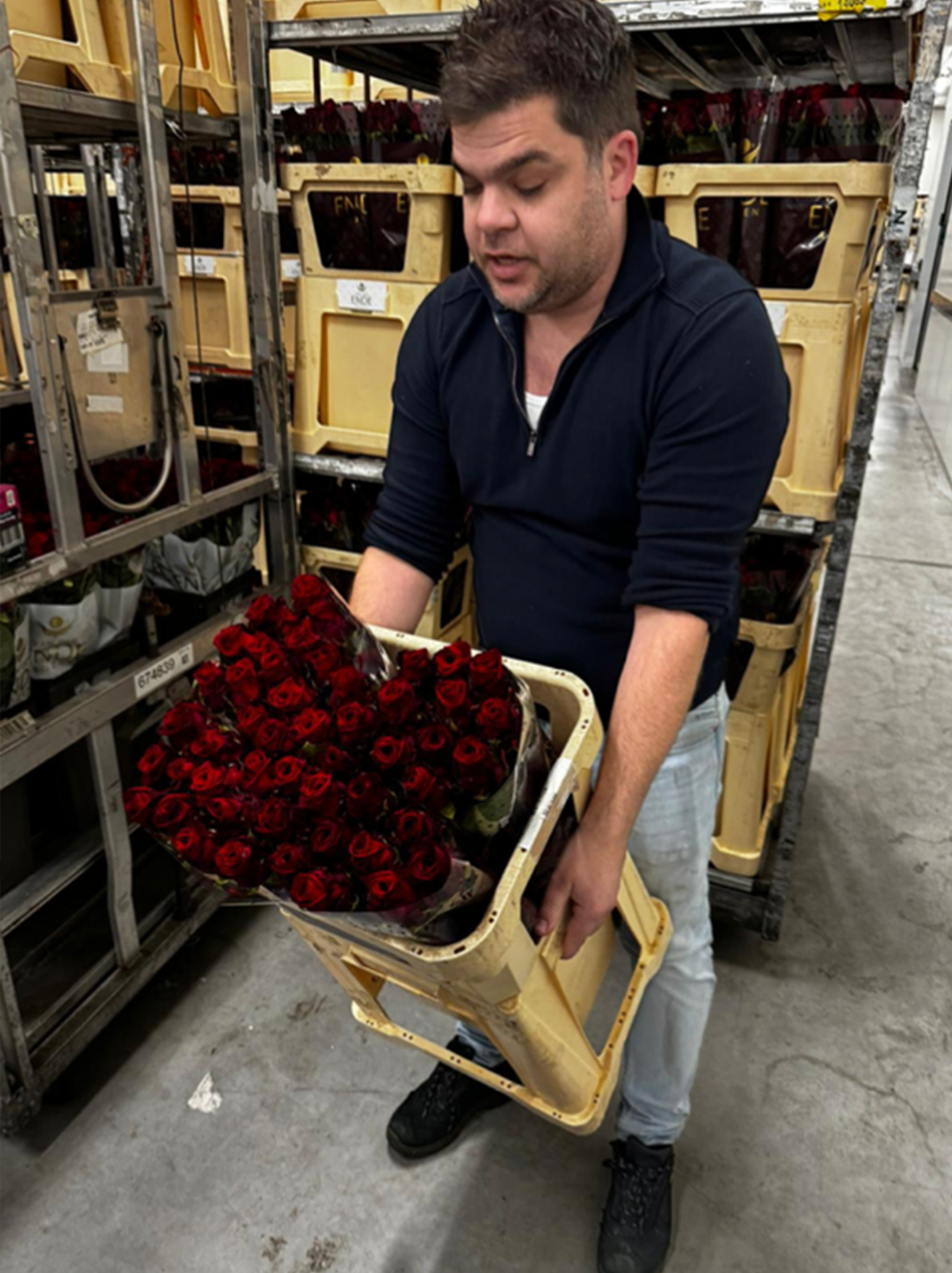